Strippers (or flux)
What is stripper ?
Also known as “flux”, the role of the (oxiding) stripper is to “clean” the surface of the parts to be brazed before the filler metal is applied.
The stripper “doesn’t strip”, but dissolves the oxide and grease layer and prevents oxidation during heating of the filler metal and brazing parts.
The stripper’s physical action reduces surface tension, improves wetting and promotes the capillary action of the filler metal.
It must melt at a temperature at least 100°C below the melting temperature of the brazing filler metal, and remain active over the entire brazing cycle.
The flux increases heat exchange between the molten alloy and the parts to be brazed: calorific action.
It must be sufficiently fluid to allow the brazing filler to be inserted into the capillary interstices of the joint.
The flux also prevents evaporation of the elements : Phosphorus, Zinc.
The flux contain irritants and/or toxic substances and should not be left in contact with the skin. At certain temperatures, they release vapors that are toxic for eyes and mucous membranes. Workshops and brazing stations must be properly ventilated. We recommend the installation of a brazing gas extraction system.
It is strongly recommended to remove all traces and deposits of flux at the end of the brazing process, so their effect does not continue over time following the brazing operation
Copper + Cooper-phosphorus brazing alloys (CuP and CuPAg) do not require strippers or fluxes, as the phosphorus included in the formulations acts as a stripper.
Ternary (Ag/CU/Zn) or quaternary (Ag/Cu/Zn/Sn) silver brazing alloys automatically require the use of a stripper to ensure good metallurgical bonding.
Flux deposition from a coated on the bare rod
Flux from a filled bare rod (tubular brazing wire)
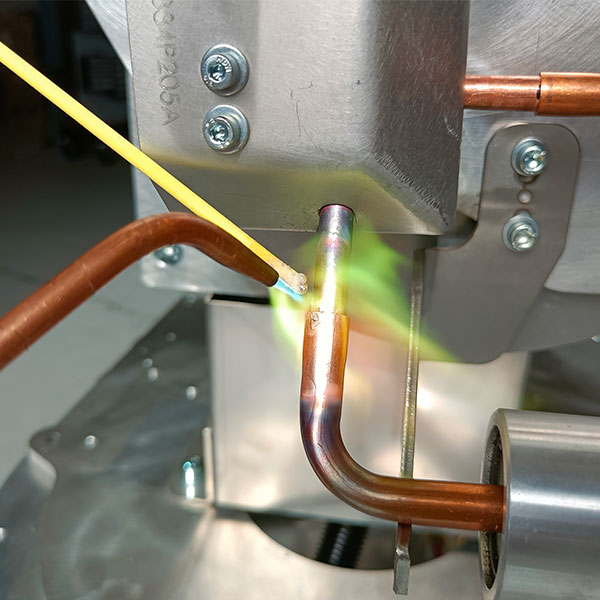
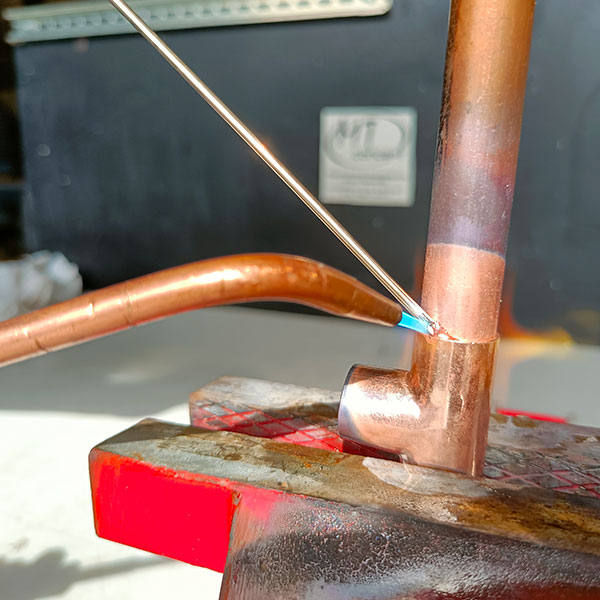
The different kinds of flux
Powders and pastes
Powders should be mixed with water before use.
For paste, the flux is usually applied with a brush in the area to be brazed.
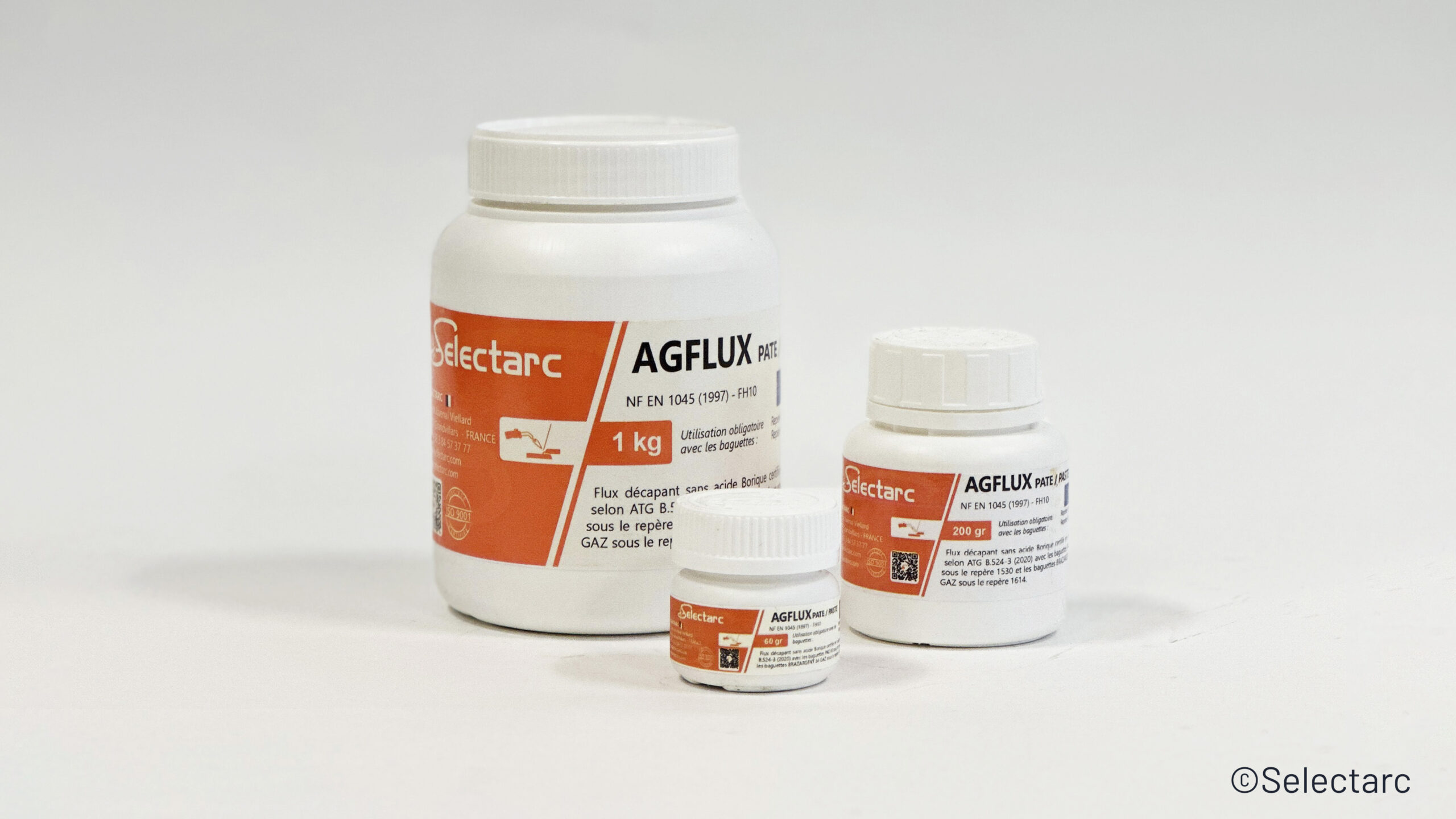
Filled bare rod (tubular brazing wire)
It flows out before the filler metal melts, allowing precise control of the amount of flux deposited.
Other benefits :
• No direct contact between operator’s skin and flux
• No coating fragility
• Reduced calorific value compared to a full bare rod
• Less off-gassing and no fizzing of flux
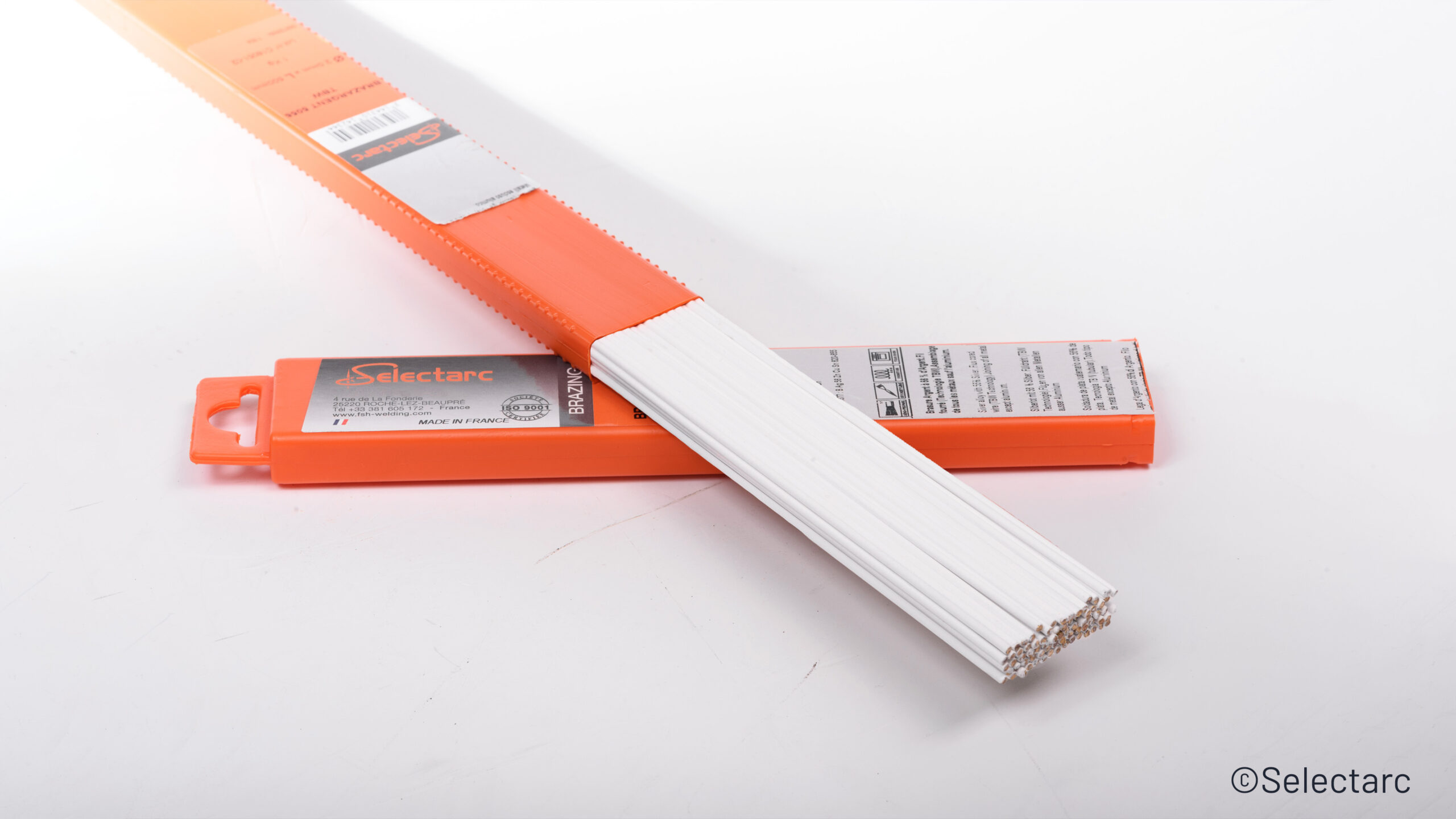
Flux coaterd rods
Flux coated sticks embed the flux in solid form directly onto the outer periphery of the filler metal bare rod.
The operator first deposits the flux, which melts at a lower temperature than the filler metal. The filler metal is deposited immediately after.
The addition of a coating ensures precise flux addition.
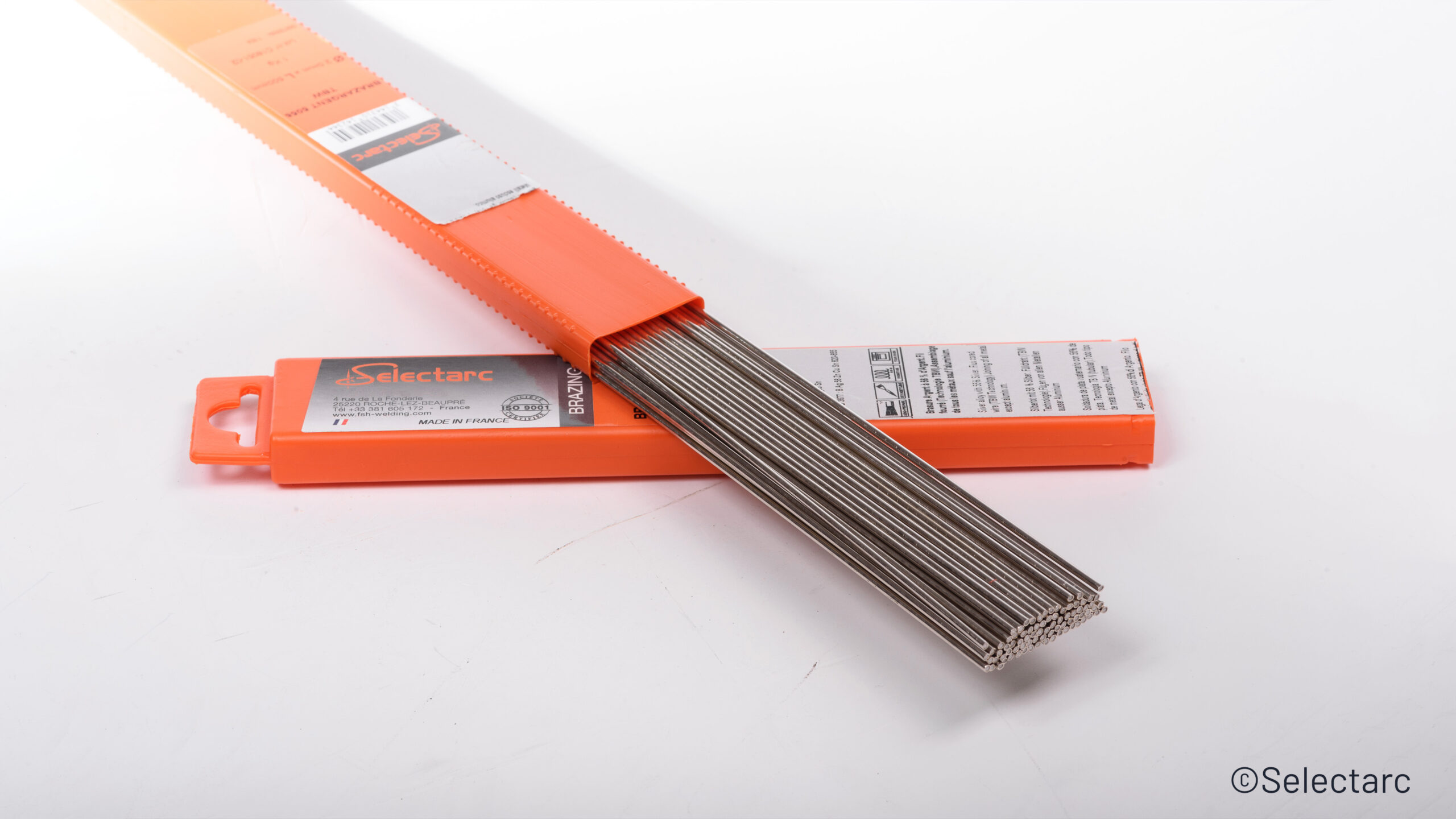