Physicochemical specificities
Three physico-chemical parameters are involved in the transition from filler metal to liquid state, and must be taken into consideration when choosing a quality brazing alloy.
Surface tension
Surface tension is a physico-chemical phenomenon linked to the molecular interactions of a fluid. It is the force required to maintain a fluid in its original state.
Example: A gerris “walks” on water. Areas where the weight of the gerris has deformed the otherwise flat water surface can be seen.
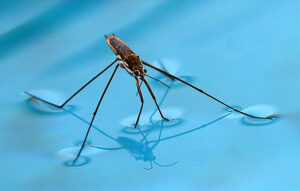
The notion of wetting
Wetting is the spreading of a liquid droplet over a solid surface. The droplet’s ability to wet is defined by the contact angle θ, which corresponds to the angle formed between the solid, liquid and vapor phases.
A wetting liquid: θ < 90°. Non-wetting liquid: θ > 90°.
Perfect wetting is characterized by zero contact angle. The liquid spreads completely over the surface of the solid.
The notion of capillarity
Capillarity refers to the ability of some fluids to propagate between two surfaces. This propagation is directly linked to the fluid’s wetting and surface tension.
“Case of the experiment with a thin tube immersed into water (wetting fluid):
The water increases its surface area in contact with the glass and decreases its surface area in contact with the air. Surface tension causes the water to rise up the tube.”
At capillary distances, gravity loses its dominant influence!
When brazing, the gap between the two surfaces must be kept under control. It is usual to guarantee a gap between 0.03 mm and 0.2 mm, depending on the type of filler metal, its coefficient of thermal expansion and the depth of the joint. Flux reduces surface tension and improves wetting.
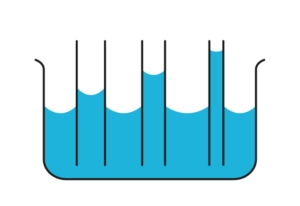
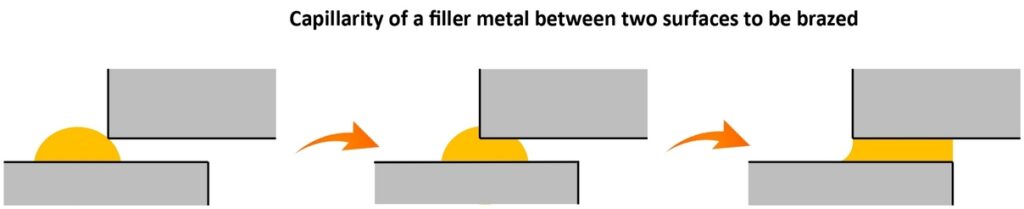
In addition to these three physico-chemical phenomena, which are essential to know and understand, there’s another important point to consider:
Heterogeneity of brazing parts
To ensure good heat distribution in the parts to be brazed, somerules must be observed:
• The two parts are not the same thickness: heating will be prioritized on the thicker part (longer heat-up time).
• The two parts do not have the same thermal conductivity: heating will be prioritized on the part with the lower conductivity (longer heat-up time).
• In the case of nesting/jointing (e.g. male/female cylinder), the female part should be heated to facilitate weld flow.