Heating technologies
There are different types of heating that allow the filler metal to reach its liquidus.
Single-gas flames
The flame is produced from a fuel gas, with the oxygen in the air acting as an comburent.
This makes the aeropropane flame very easy to use and very economical.
This type of flame provides less energy than a bi-gas flame, resulting in lower heat levels. It is essential, consequently, to choose a brazing alloy with a melting point less than or equal to 730°C.
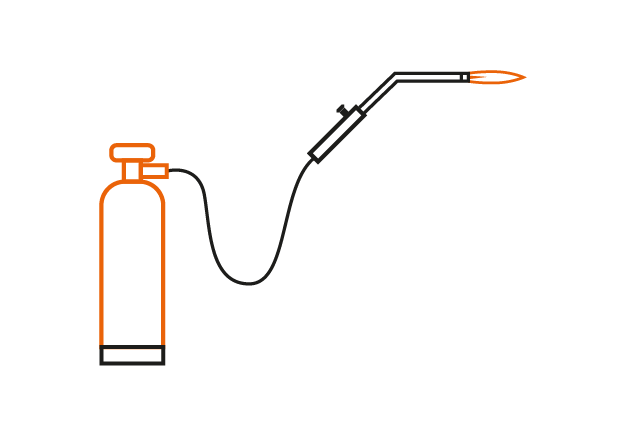
Dual-gas flames
A dual-gas flame is produced by combining a fuel gas and an comburent gas.
The comburent gas used is oxygen, stored under pressure and expanded to allow mixing.
The fuel gas can vary, including acetylene, propylene, propane and natural gas.
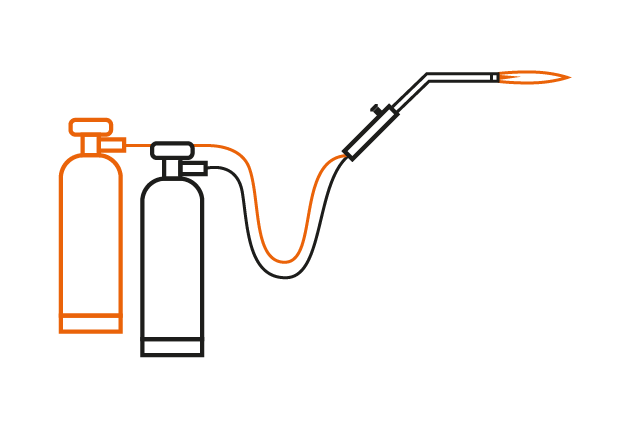
The oxy-hydrogen flame
The oxy-hydrogen flame is a mixture of oxygen and hydrogen, obtained by electrolysis of water. This process involves passing an electric current through the water molecule (H2O) to break it down into oxygen and hydrogen gas.
This flame, 10 times more conductive than acetylene flame, allows to heat the parts faster, exposing them less time to heat, which reduces their oxidation. Result : less deposits of scale and simplified cleaning.
Hydrogen, which does not contain carbon atoms in its chemical composition, produces a combustion without CO2 emissions. It is a clean combustion gas, significantly reducing the environmental impact of brazing applications.
In summary, this flame offers many advantages in terms of productivity, safety and decarbonisation.
Incorporating BULANE’s Dyomix® electrolysis technology, the Dyoflam® soldering stations generate on-site and on-demand a clean and high performance oxy-hydrogen mixture without storage or transport, eliminating the constraints associated with gas cylinders and their supply chain.
For more information about this technology, please contact our partner BULANE.
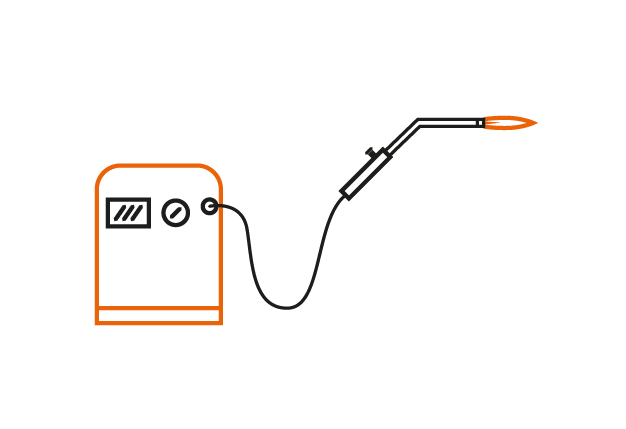
Induction
Induction brazing uses an inductor, consisting of a coil with alternating current that creates an electromagnetic field.
This process enables many ferromagnetic materials to be brazed with precision, speed and repeatability.
It is commonly integrated into automated production lines.
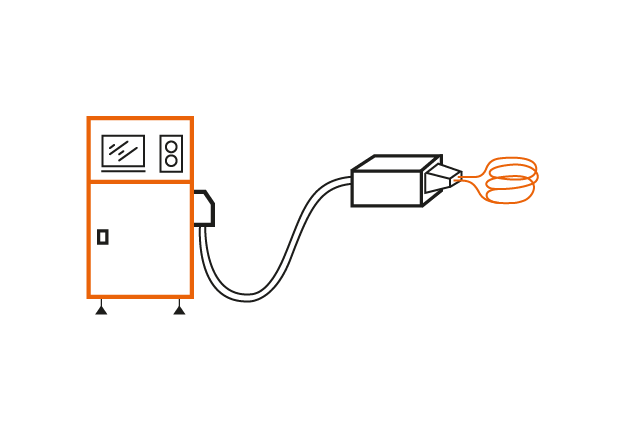
Furnaces
- Brazing furnaces devide into two main categories:Continuous furnaces maintain a uniform temperature at each point, with slight variations.
- Very commonly, products enter at one end and exit at the other.
- Batch furnaces follow a predefined heating cycle, with the temperature evolving with each stage. Products remain stationary during the process.
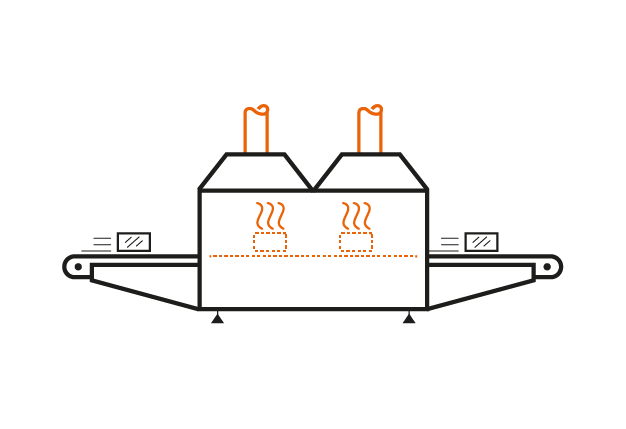
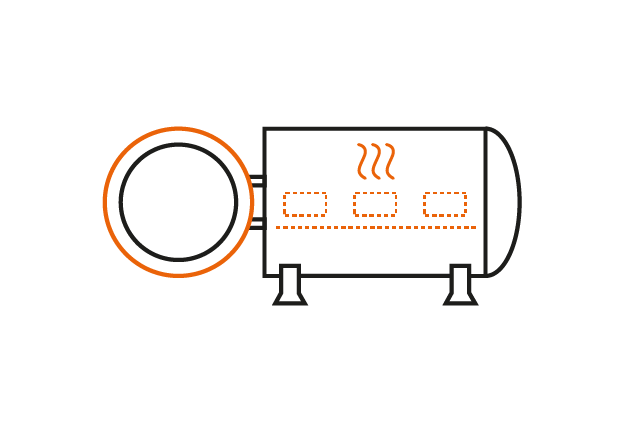
The parts to be brazed, previously assembled with a brazing alloy, are introduced into the furnace where they are heated. Vacuum brazing is often used with this equipment, particularly for brazing complex shapes.
Laser brazing
Laser brazing is a non-contact process, often associated with weld brazing.
The laser beam penetrates the material and melts the filler metal. This technology is particularly common for body assembly in the automobile industry. It is generally used to join galvanized steel sheets or lightweight aluminum parts.”
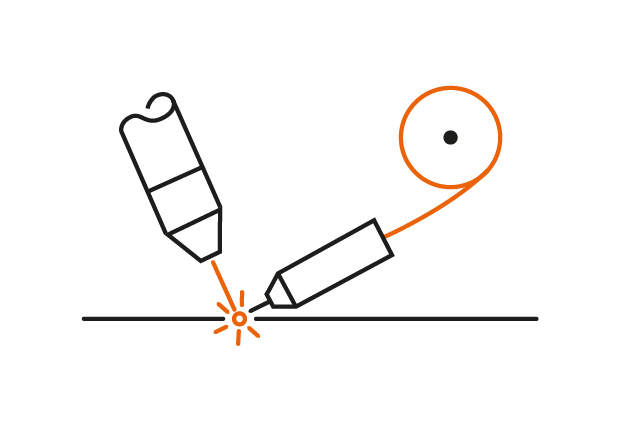
Other heating processes
There are many other brazing processes. These include:
- The reflow brazing for brazing electronic components to printed circuit boards using hot air
- The wave brazing for brazing electronic components to printed circuit boards by projecting molten filler metal.
- Heating clamp
- Soldering iron
- Hot air gun